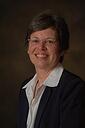
Guest Blogger: Melanie Hodgdon is a Certified QuickBooks ProAdvisor who has been providing financial analysis and QuickBooks training for contractors since 1994. She’s the co-author of A Simple Guide to Turning a Profit as a Contractor. Melanie and Shawn often coordinate their efforts when helping remodelers develop financial systems for their businesses so they serve the contractor, not just their accountant.
Understanding and Including General Production Costs in Your Estimates
Estimators are pretty good about including costs for permits, materials, subs, and equipment rental in their estimates. And the really topnotch ones are also adept at estimating the amount of labor time based on knowledge of what their crew(s) can produce. But there is another element that often eludes even the most careful of estimators: the cost of those “necessaries” that will be used on a job but not easily assigned to specific jobs.
These include things like:
Bits
- Blades
- Rags and other cleaning supplies
- Sanding disks and sand paper
- Trash bags
- Small tools
- Dust masks
- Assorted fasteners
- Caulking and adhesives
- Pencils, markers and chalk
Here are some more candidates:
Cost to repair and maintain tools and equipment
- Cost to maintain a jobsite trailer
- Propane for the space heater
- HEPA filters
- Bungies, ropes and tie downs
- Trash barrels or bins
These can be considered General Production Costs and you should have a method to allow for them in the job price.
Two ways to price your work
Basically, pricing consists of identifying the actual cost of X and then adding a markup. The purpose of the markup is to allow the selling price to cover not just what X costs, but also it’s fair share of the company overhead, with enough left over to contribute to company profit.
Option A: Include in the estimate
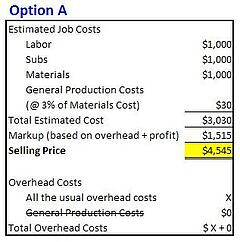
When you include an allowance for General Production Costs in your estimate, you increase the predicted cost of the job. When you apply a markup to the cost, you will also be marking up the predicted General Production Costs. Because you are charging your customer for the cost (income account), the matching cost should be considered Cost of Goods Sold.
For many contractors, including an allowance for these costs in the estimate will increase the likelihood that the costs will be covered.
Option B: Include in the markup
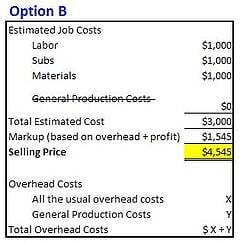
If you consider General Production Costs as being part of the cost of doing business (overhead), then you will account for them by increasing your markup on the job.
Ideally, both methods will result in the same selling price. However, in my experience, far too many contractors decide on a markup based not on the financial requirements of their company, but rather on a figure they found in an article, or what scuttlebutt tells them their competition is using. This WAG (wild ass guess) approach decreases the likelihood of capturing these costs in the markup.
Why I typically recommend Option A
Also, as companies have diversified with changes in the economy, the type of work they do has also changed in many cases. Burying these costs in overhead can make the changes less obvious than placing them in Cost of Goods Sold where significant changes are more likely to be spotted. For example, companies performing lots of RRP work might see a significant increase in these costs due to the requirement for filters, respirators, contractor bags, signage, duct tape, Tyvek suits, etc. The effect on the gross margin (when these costs reside in Cost of Goods Sold) might be noticed more quickly and reliably than remembering to deliberately dig into the overhead accounts to find and monitor them.
Estimating vs. job costing considerations

Once your General Production Costs are part of Cost of Goods Sold, an allowance for the inevitable cost can be included in the estimate. This means that you will charge for them as part of your pricing strategy. However, because of their very nature, you won’t be able to attribute them to individual jobs, so when you look at job cost reports, you will not see an “actual cost” for these items, making the jobs appear slightly more profitable than they probably are. The achieved margins of all the jobs will look higher than the overall achieved margin from the Profit and Loss Statement since the Profit and Loss Statement will contain the dollars spent on General Production Costs and the individual job reports won’t.
How to calculate General Production Costs for estimating purposes
The simplest way is by comparing General Production Costs with Materials costs. Express the relationship as a ratio or percentage. For example, if in the last twelve months you spent $500,000 on materials and $8,000 on General Production Costs, you will need to add 1.6% ($8,000 ÷ $500,000) to your estimate to cover them. When estimating, this figure can be added as a line item as shown in the sample estimate template below.

Screen shot from Shawn's new estimating Template
Final thoughts
Each job has enough surprises in it. Why not at least plan your sell price to include an allowance for the costs you know you can count on?

Need help with General Production Costs?
Call or Email Shawn today.
Do it now so you can be confident you are pricing your spring and summer projects correctly!