RRP Rule Interior Containment General Requirements:
The RRP rule requires that dust and debris be controlled in the work area while working in homes built prior to 1978 unless all effected components of the renovation are properly tested and lead is not found. You can find information about the legal definition of lead paint and the accuracy of testing methods here.
In general, renovations that involve only a small amount of paint disturbance create less dust than jobs that involve larger areas of paint disturbance. However, in addition to the size of the area of paint disturbed, the work practices (e.g., sanding) and equipment used will also affect how much dust is created and how the dust migrates. The location of the work activity also has a bearing on the amount of dust that is distributed. For example, small areas of ceiling work can spread dust over the entire room and are very difficult to control.
Required containment is similar for all jobs, but jobs that generate more dust and debris may require protection of larger areas. While the Rule does not require vertical containment, such systems may be helpful in limiting the size of the area affected by the work and may reduce the area that must be cleaned at the end of the job. Pre-engineered containment systems (purchased and home-made) are very helpful in cutting time spent on the job erecting containment and are easier to install than hanging plastic sheeting with tape. These systems also allow the contractor to create a sealed room within a room where the dust can be completely contained to a limited and controlled area. Click here to download a helpful list of tools and supplies for RRP work.
Remember, you are responsible for making sure that dust and debris remain inside of the contained work area. When planning containment, keep in mind how, how much, and where the work practices to be used will create dust, and plan accordingly. This information should also be considered when estimating the cost to do the work.
General requirements for interior containment:
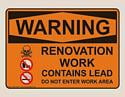